The 5 Pillars of Safety Communication: Lessons from the PDX Next Expansion
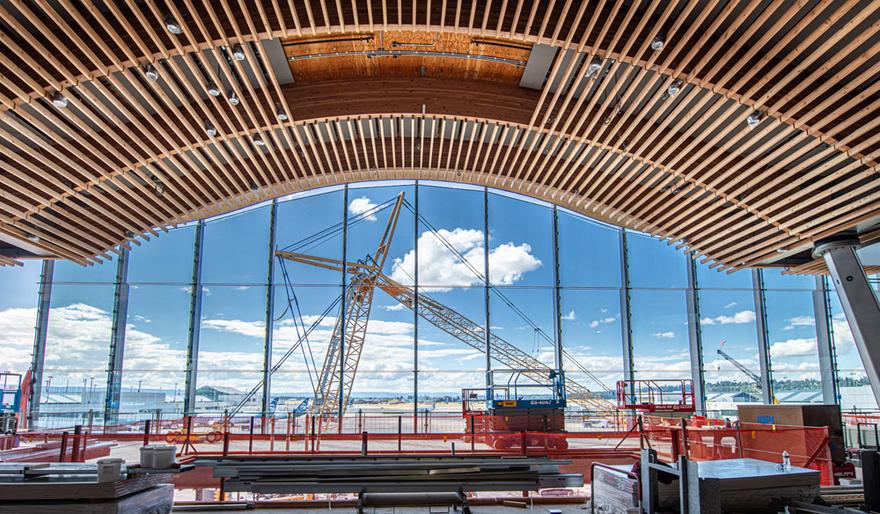
If you’ve ever experienced frustration, confusion, or even danger on a jobsite, chances are communication was at the root of the problem. In my work with construction teams, I’ve seen time and again how safety breakdowns often stem from unclear expectations, missing information, or a lack of dialogue between teams.
The Portland International Airport (PDX) Next Expansion is a prime example of how strong communication can elevate safety and efficiency. In an active airport environment—with thousands of passengers, tight security measures, and a maze of subcontractors—the risks were enormous. Yet, thanks to five key communication strategies, the project maintained an outstanding safety record while staying on track.
These principles don’t just apply to massive infrastructure projects—they’re the foundation of any high-performing safety culture. Let’s break them down.
1. Consistent Messaging
From day one, the leadership team drilled a single, clear safety message into every level of the workforce:
“No milestone is worth compromising a single worker’s safety.”
This wasn’t just lip service—it was reinforced in onboarding manuals, digital newsletters, signage throughout the site, and site-wide announcements.
One manager, Sarah Tan, reinforced this with a simple mantra at every briefing: “Check yourself, check your teammate.” Soon, workers began repeating it naturally—reminding each other to stay alert.
How often does your team hear its safety message? Monthly? Weekly? Daily? The frequency of communication makes all the difference.
2. Make Safety Information Accessible
With electricians, steelworkers, HVAC techs, and dozens of other trades on-site, everyone needed quick, clear access to safety protocols. The PDX team made information accessible by:
- Posting multi-lingual safety boards at every major entry point
- Using color-coded maps to highlight restricted areas
- Placing QR codes linking to real-time safety updates
By ensuring safety information was available in English, Spanish, Russian, and Vietnamese, every crew member felt respected, informed, and engaged.
How easy is it for your team to access real-time safety information? If workers can’t get the answers they need quickly, confusion and mistakes follow.
3. Daily Safety Briefings
Every morning at 6:30 a.m., teams held a five-minute safety briefing—short, focused, and action-driven.
One morning, a crane operator flagged an incoming windstorm. Because everyone was gathered for their usual safety huddle, the team adjusted schedules and likely prevented multiple near-misses.
Why it worked:
- Briefings were predictable—everyone knew when and where to show up
- They addressed real-time risks—not just general safety talk
- They created a culture of awareness—workers looked out for each other
Does your team have structured, daily safety briefings? If not, what would it take to start?
4. Regular Check-Ins to Catch Issues Early
Beyond the morning huddles, site supervisors did midday pulse checks—walking the jobsite, talking with crews, and listening to concerns.
One major win? Forklift drivers noticed that travelers were accidentally walking through active work zones. Because supervisors caught this early, they adjusted barricades before an accident could happen.
When was the last time your leadership team did a walk-and-talk safety check? If you wait for problems to be reported, you may already be too late.
5. Create a Feedback Loop—And Act On It
Many leaders say they’re open to feedback, but in reality, workers hesitate to speak up—fearing job consequences or being ignored. PDX solved this by offering:
- A text-based safety hotline
- An anonymous QR code suggestion box
- A physical comment dropbox in a high-traffic area
A veteran electrician, noticed temporary lights weren’t being tested properly after power outages. He used the anonymous hotline to report it, and within 24 hours, a new verification process was in place—dramatically reducing electrical hazards.
What feedback channels does your team offer? If you’re not getting regular, actionable safety input, it’s time to rethink your approach.
Communication Saves Lives
The PDX Next expansion didn’t just protect workers—it set a new standard for communication-driven safety. The results?
- Minimal safety incidents despite working in an active airport
- Higher crew morale—workers felt heard and valued
- Recognition from industry leaders for their safety protocols
If you take one thing from this story, let it be this: Safety doesn’t have to be complicated—but it MUST be communicated.
Now it’s your turn—what’s one safety communication strategy that has worked for your team? Share your best communication hack in the comments on our Instagram post with #SafetyThroughCommunication. Let’s learn from each other and keep more workers safe.