Practicing Preparedness: The 4 Keys to Building a Safety-First Mindset
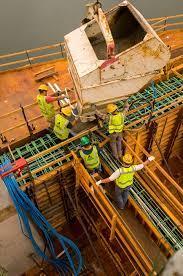
Culture and communication lay the foundation for a strong safety culture—but without preparedness, even the best intentions fall apart under pressure. Preparedness isn’t just about having the right gear; it’s about training ourselves and our teams to respond with confidence, skill, and speed in any crisis.
Preparedness isn’t just having a manual or a stocked first-aid kit. It’s a mindset. It’s about ensuring that when the unexpected happens, your team knows exactly what to do—without hesitation.
A powerful example of this comes from the SR 99 Tunnel Project in Seattle, which replaced the aging Alaskan Way Viaduct with a modern tunnel under the city. This project was high-risk—workers excavated beneath an active downtown, navigated unstable ground, and faced the ever-present danger of seismic activity.
Construction leaders knew they couldn’t rely on luck. Instead, they practiced preparedness through four key tactics. These same principles can protect your team, your projects, and your bottom line.
1. Regular Safety Drills: Train Like It’s Real
When an emergency hits, your team won’t rise to the occasion—they’ll fall to the level of their training. If they haven’t practiced, they’ll panic.
On SR 99, crews ran quarterly emergency drills, simulating scenarios like:
- Earthquakes and tunnel collapses
- Water intrusion and flooding
- Hazardous material spills
These drills weren’t just for show—they were multi-agency exercises with firefighters and emergency responders. By rehearsing real-world crises, workers learned to act fast, follow protocols, and trust their training.
Yet, according to a recent poll, 55% of construction workers feel they need more safety training. That means over half of our workforce is underprepared for the very risks they face daily.
Ask Yourself: When was the last time your team ran a hands-on safety drill? If you can’t remember, it’s time to schedule one.
2. Continuous Education: Safety is a Skill—Not a One-Time Lesson
On SR 99, safety training wasn’t a one-and-done event. It was a daily priority.
- Pre-shift briefings focused on job-specific hazards.
- Specialized training taught crews how to tunnel safely in a seismic zone.
- Workers learned to identify early warning signs of ground movement or equipment failure.
This consistent education made a critical difference. Instead of being caught off guard, teams were trained to spot risks before they became disasters.
Too often, safety training happens once at onboarding and never again. But safety isn’t a checkbox—it’s a skill that needs sharpening.
Ask Yourself: How often does your crew receive updated safety training? If it’s not ongoing, gaps will form—and those gaps lead to accidents.
3. Autonomy: Empower Workers to Stop Work—No Questions Asked
One of the most critical moments on SR 99 came when an equipment operator noticed unusual water pressure after Bertha, the tunnel boring machine, resumed digging.
Instead of waiting for permission, he immediately stopped work. Investigators later found a small seal breach—one that, if ignored, could have led to catastrophic flooding.
That operator’s quick action saved lives and prevented millions in damage.
Prepared teams don’t wait for permission to act. They know they have the authority to stop work when something feels off. But in many companies, workers hesitate—afraid of slowing down production or facing backlash.
If your workers don’t feel empowered to act on their instincts, your safety culture is broken.
Ask Yourself: Do your people know—without a doubt—that they can stop work if they sense danger? Have you reinforced that expectation enough?
4. Support & Resources: Give Your Team the Tools to Succeed
Preparedness isn’t just about what workers know—it’s about what they have access to. The right training is useless if the right resources aren’t available in a crisis.
SR 99 ensured workers had:
- On-site ‘Safety Pods’ stocked with first-aid kits, updated protocols, and emergency tools.
- 24/7 real-time sensors monitoring ground movement and water intrusion.
- Supervisors trained in crisis management to lead under pressure.
These resources allowed workers to act fast instead of scrambling for solutions in an emergency.
Think about your own job sites. If disaster struck, would your crews know where to find emergency tools? Would supervisors know how to lead with clarity and calm? If the answer isn’t a confident “yes,” there’s work to do.
Ask Yourself: Are safety resources clearly available and maintained? Do your supervisors know how to lead in a crisis?
Preparedness Saves Lives—Are You Practicing It?
The SR 99 Tunnel Project didn’t leave safety to chance. They trained, educated, empowered, and equipped their workforce to handle the unexpected. That’s why they maintained a strong safety record—despite the project’s immense risks.
If you take one thing from this, let it be this:
You don’t want your team figuring out safety in the moment. Train them today so they can respond without hesitation tomorrow.
Your Quick Win Challenge:
This week, schedule one preparedness drill or safety talk on a real-world job site hazard. Even 10 minutes can make the difference between crisis and control.
What’s one way you’ve prepared your team for emergencies? Share your best safety preparedness tip in the comments on our Instagram post or with #PreparedForSafety. Let’s keep the conversation going and keep each other safe.